Importance Of Systems In The Real estate Industry
Many Will Agree, Real Estate Industry in India is one of the most disorganised Industries. It requires embracing many systems to become more organised and efficient. This is the excerpts of one of the chapters from my upcoming book.
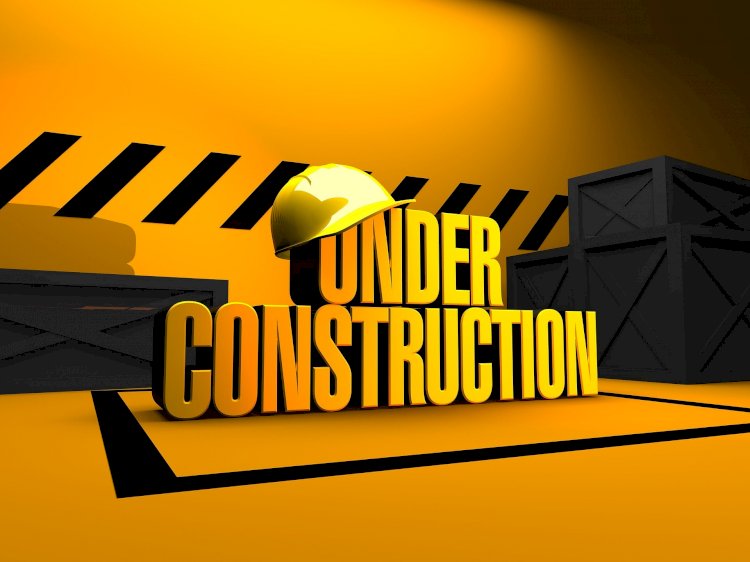
Efficient & effective construction techniques are critical in raising productivity, increasing profitability,
meeting schedules, and improving safety. While achieving improvements in profits is the immediate objective of all, be it a developer or a contractor, they must not lose sight of quality and product safety. The structural frame holds up the building, and it is imperative that it is constructed with the necessary
strength and the required durability to comply with the aims of the designers. Imagine the cost & time implication on the project for redoing the defective work. If you can realise that, doing first time right quality work will come second nature of yours very easily.
The structures that we put up in a brief moment must last a lifetime. The design stage is the beginning. How we construct and how we maintain them determines the health of our buildings. Strength and durability are considered and actively pursued at all stages. In our education system emphasis is put on design with little acknowledgement paid to the construction site. As we mature and our experience grows, we respect the construction stage, more and more measures are taken to ensure that we build correctly and to the requirements of the designer.
In reinforced concrete construction, unlike the use of steel, where the components are all manufactured in controlled environments and erected on-site, the process is much more complicated. Concrete is made up of cement, sand, coarse aggregate, and water in predetermined portions. It has to be properly batched, mixed, compacted, and cured to give us the strength and durability we desire. The concrete must protect the reinforcement with which it forms a whole system. Anything can go wrong. The result is disastrous. The only way to prevent things from going wrong is by having systems in place, by monitoring & control.
Laxity in the degree of control at the construction stage would result in defects due to poor workmanship, incorrect use of materials. Defects give rise to cost in maintenance. Maintenance alone cannot correct the inherent defects built into the buildings, and it is for this reason that we must not only exercise good quality control but have systems in place to avoid unwanted issues arising and causing a delay in the project and incur cost overrun of the project. In fact, in today’s world, maintenance and repairs to the structure at most times surpass the original cost of construction, and now with the responsibility of maintaining the structure for 5 years being on the developer, it is even more imperative that the structure
is built right the first time with the highest quality possible to reduce maintenance and repair costs.
TYPICAL SITE CONTROL SYSTEM:
Typical site quality inspection for concrete construction relies on the cube results to determine the in-situ strength. In the pre-concreting stage, the emphasis is mainly on detailing & cleanliness. During concreting, the control is concentrated on random cube taking & slump tests. While doing concreting,
much of the control is left to the contractor. In post concreting the inspection is on formwork striking period and curing of concrete. This typical control system is very much dependent on the contractor’s competent personnel. Improved Control System
There are 3 basic stages for controlling the concrete quality on site. This system comprises of pre-concreting, concreting, and post concreting inspections. The following summarises the possible control areas at different stages of work. In order to upgrade the awareness of engineers on the importance of Concrete Technology and to bridge the lack of formal training on the subject to Engineer-In-Charge, inhouse training in “Basic concrete Technology” and “Good Concreting Practices” should be given annually. This training should also extend to the contractor’s staff. Special training should also be given to a group of selected Quality Assurance Engineers who make regular but random inspections on various construction sites. This training results in a group of professionals who can appreciate and implement the inspection system much more effectively.
What's Your Reaction?
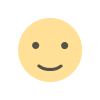
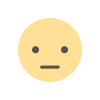
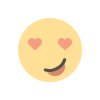
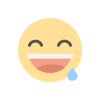
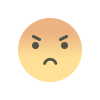
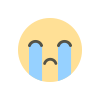
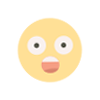